Do you have any questions?
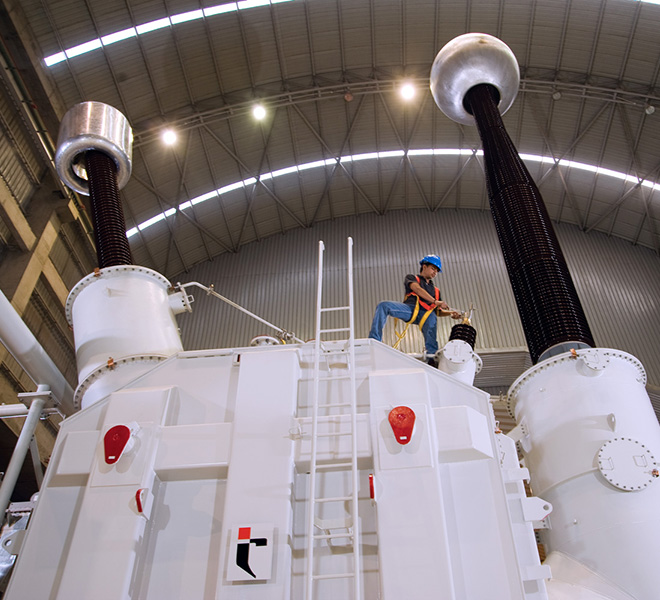
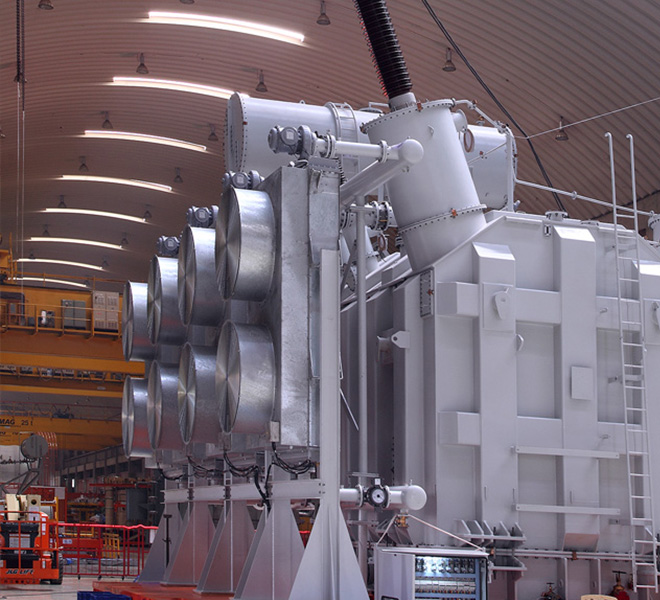
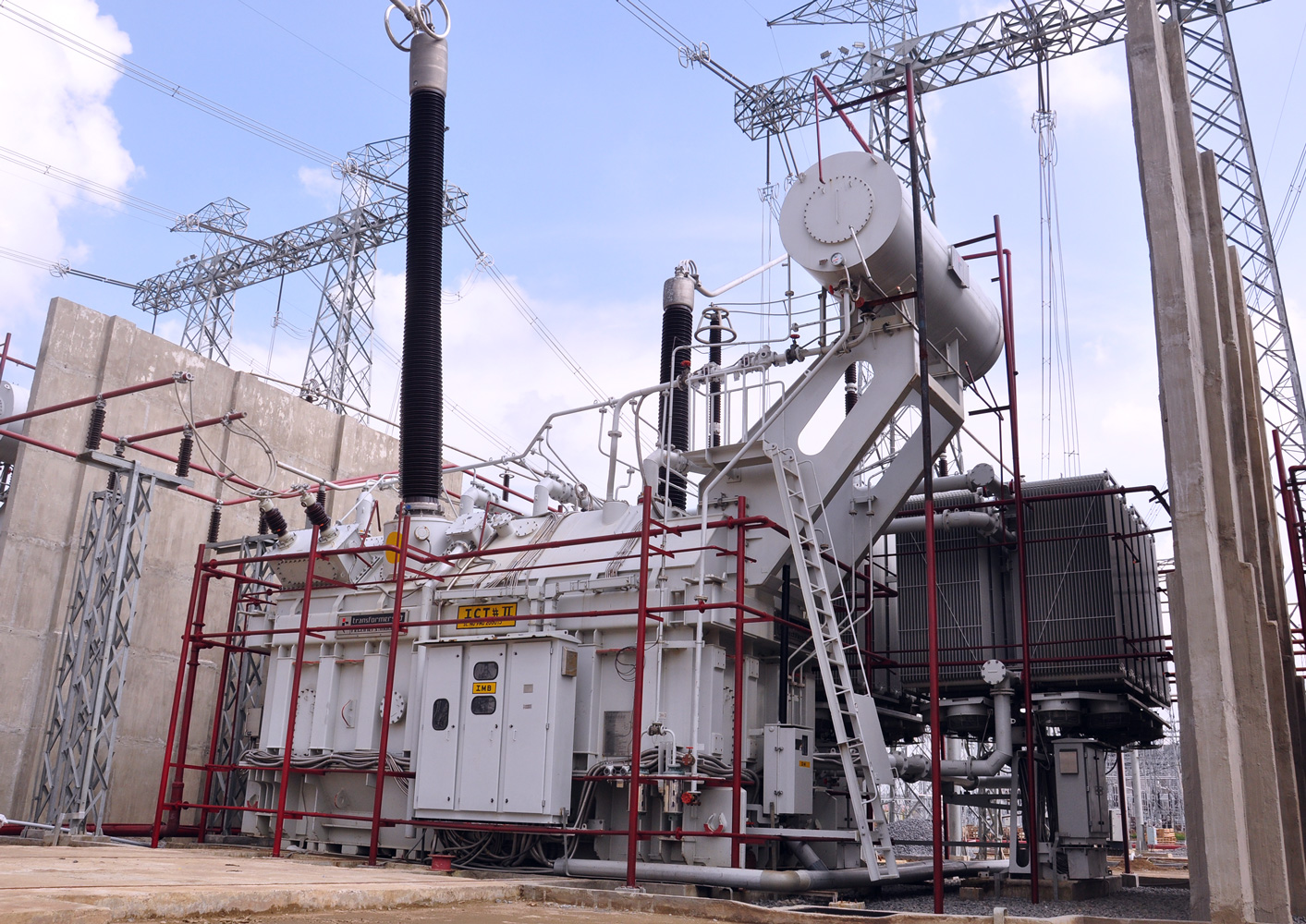
Overview
TARIL offers a wide range of power transformers from medium to ultra-high voltage (1200 kV AC) and from small (5 MVA) to very large power ratings (500 MVA) tailored to meet global customer’s needs.
Latest technologies in design, measurement and testing tools are applied in TARIL transformers to ensure each transformer meets and exceeds the latest industry standards, as well as operational and customer specifications. Sophisticated and extensive simulation tools are used at TARIL to prove the product design and ensure superior product performance in the field. Reliable design is supported by state-of-art manufacturing and extensive quality control. Power transformers designed and manufactured by TARIL provides exceptional performance, quality and reliability.
Sustainability goals
We offer the most complete industrial solutions in the century for the research, design & development of materials.
Guaranteed quality
The procedures and techniques that are used during the building process
Product Range
TARIL Power Transformer product range includes conventional as well as green power transformers. Power Transformer product range includes,
Auto transformers offers economical optimized solution for interconnection in grids while compared to conventional two winding power transformers. TARIL offers wide range of Auto transformers including constant or variable flux regulation, with or without tertiary winding in both single phase and three phase combinations upto 500 MVA and 1200 kV class.
The generator step-up unit transformers have delta-connected LV windings energized by the generator voltage and star connected HV winding connected to the transmission grid. TARIL offers wide range of generator step up unit transformers suitable for thermal, hydro and nuclear plant applications upto 1000 MVA, 765 kV class.
Small and medium power transformers are used mainly to evacuate solar and wind power generated to the main grid as well as catering plant loads. TARIL offers wide range of small to medium power transformers with tailor made requirements upto 150 MVA and 400 kV class.
The trackside traction transformers are used for stepping down the grid voltage levels for the railway network. Track side transformers undergoes severe duty conditions include overloading and frequent short circuit during service life. TARIL offers wide range of trackside traction transformers suiting railway requirements upto 50 MVA, 220 kV class.
TARIL Advantage:
- Dynamic Short circuit tested designs
- Attractive delivery
- Excellent service record
Unit and station auxiliary transformers are used in thermal stations for feeding auxiliary power to various equipment’s. TARIL offers wide range of unit and station auxiliary transformers upto 125 MVA.
TARIL Advantage:
- Dynamic Short circuit tested designs
- Attractive delivery
- Excellent service record
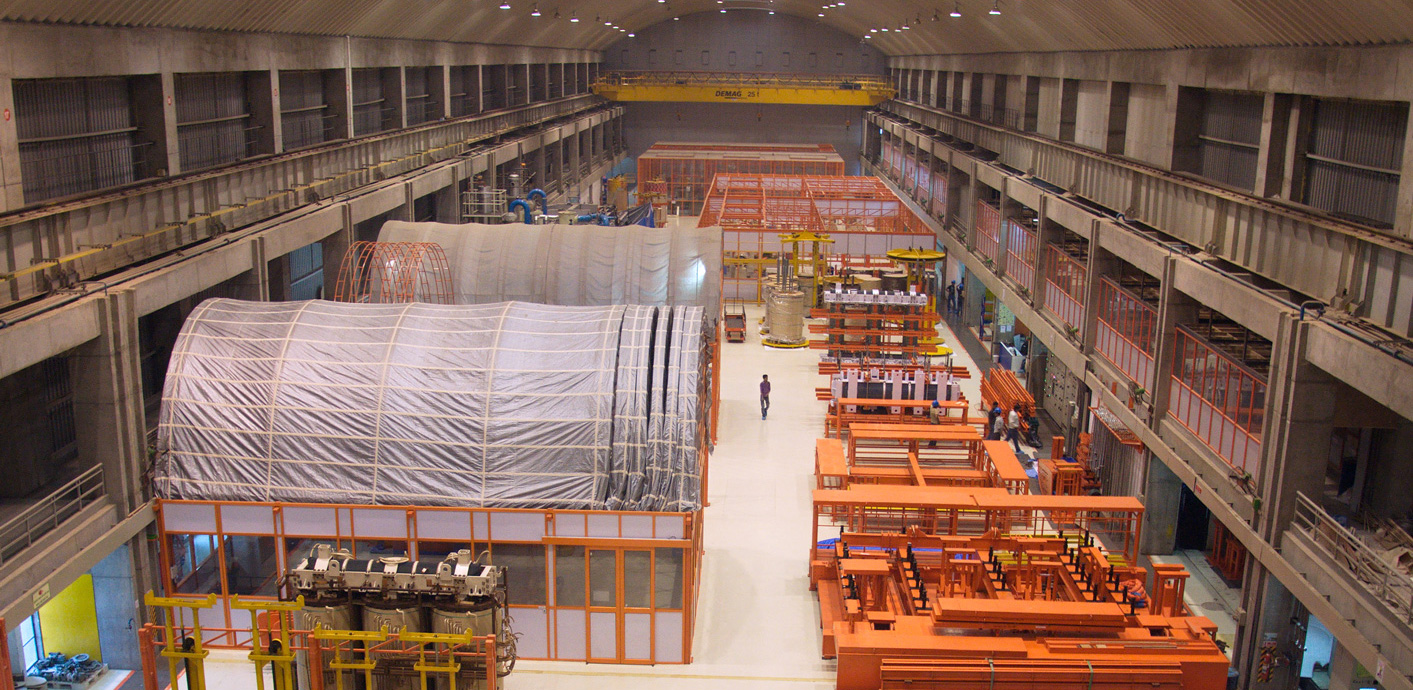
Overview
T&R’s ultramodern manufacturing facility in Moraiya, an industrial area near Ahmedabad, is built up on an area of 14,000 sq. mt. and has the capacity to produce 16,000 MVA per annum. T&R has now leapfrogged to an elite league capable of manufacturing and testing 765 KV Transformers.
Plant is certified for ISO 9001:2015, ISO 14001:2015 and ISO 18001:2018
Features
1. Plant capacity to produce 16,000 MVA per annum.
2. Plant is capable to produce and test 765 kV Transformers and shunt reactors.
3. Maximum crane capacity is 300 T.
4. Epoxy coated floor in complete shop floor suitable for air cushion transporter movement.
5. Built up area 14,000 Sq. M.
6. In-house fabrication facility to manufacture 500 MVA Transformer tank.
Testing Facility
1. 30 M roof height test lab.
2. Impulse test setup up to 2800 KVp.
3. Transformer loss measuring system of 100 KV, 4000 A with accuracy of 20 ppm.
4. Capacitor bank of 50 MVAR.
5. Testing transformer of 6000 KVA, 100 KV.
6. Voltage regulator of 3 MVA, 0-11 KV.
7. 25 Amps resistance meter.
8. PD measurement system.
Process / Equipment
- Winding and core–coil assembly in fully dust controlled environment with air conditioners.
- Air showers are installed at three entries to prevent entry of dust.
- Automated rolling shutters to restrict entry of dust & foreign objects
- Six nos.Vertical winding machine of 20T SWL capacity
- Six nos.Horizontal winding machines of 20T & 10T SWL capacity
- Windings sizing with iso-static press, fitted inside winding autoclave
- 2 nos.Winding autoclave with VPD setup.
- Core building on core building cradles 9. Crimping tools for lead connections.
- 2 Nos. of Autoclave with VPD set up for active part drying. VPD capacity is 350 KW.
- Tanking activities are being done in controlled atmosphere in a pit having AHU with air conditioner to control humidity and temperature.
- Oil filter machines of 20 Kilo Liters per hour and 15 kilo liters per hour capacity.
- Oil storage capacity of 300 KL.
- Fabrication shop is equipped with CNC plasma cutting, CNC press brake, shot blasting plant, paint booth etc.

Overview
T&R’s Changodar unit (15 kms from Ahmedabad) functions as its main works facility and covers an overall area of 25,000 sq. mtrs with a built up area of 7,200 sq. mtrs.
Plant is certified for ISO 9001:2015, ISO 14001:2015 and ISO 18001:2018
Features
1. Plant capacity to design, manufacture and test transformers up to 160 MVA .
2. Plant is capable to produce and test 245 kV Transformers.
3. Annual manufacturing capacity of 7000MVA per annum.
Testing Facility
1. Equipped with state of the art testing facilities to perform all routine and special tests for transformers up to 160 MVA/220 KV class.
2. 1200 kvp impulse generator for carrying out impulse test.
3.Capacitor Bank for Load Loss Test for higher capacity.
4. Voltage Divider for higher Voltage Test
Process / Equipment
- 16 Horizontal winding machines of capacity ranging from 5T to 10 T and 3 Vertical winding machines of 10 T capacity.
- 08 Horizontal Winding machines and 03 winding machines are installed in a room with positive pressure.
- There are 02 Nos. of VPDs for processing of active parts, 01 no. of vacuum drying plant for processing of Separate Phase Assemblies and 01 no. of vacuum oven for processing of windings.
- 200T capacity hydraulic press for pressing of windings.
- Low humidity room for final pressing of active part before tanking
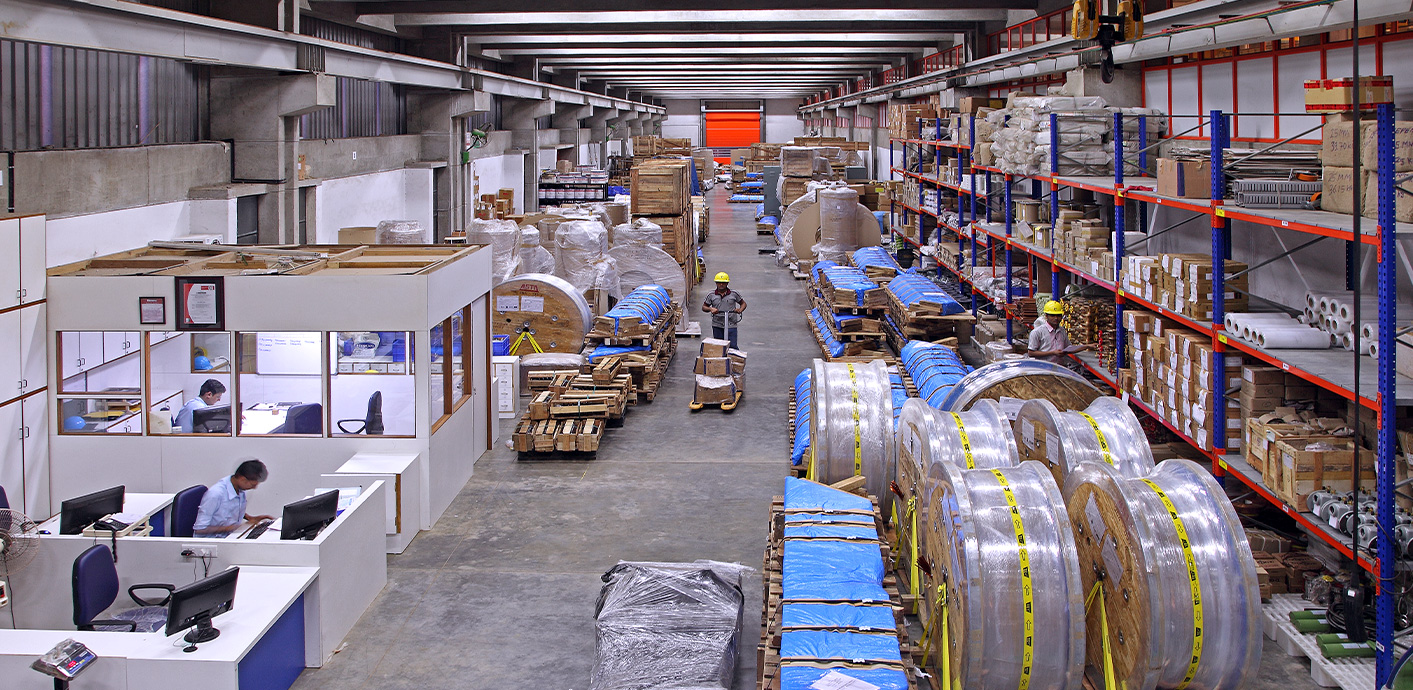
Overview
Plant is certified for ISO 9001:2015, ISO 14001:2015 and ISO 18001:2018
Our Odhav plant has a manufacturing capacity of manufacturing 1200 MVA/per annum, and a testing capacity up to 10000 kVA – 66 kV .
The unit is dedicated to manufacture Distribution transformers and Furnace transformers. Apart from distribution and furnace transformers, we have an experience of manufacturing hermetically sealed transformers with corrugated tanks, earthing transformers, auto transformers, earthing reactors and power transformers at the Odhav Plant We have our own tank manufacturing unit in Odhav at a walk able distance from the main plant, which can cater 100 % requirement of the Transformer division, which gives us better control on quality
Features
1. Plant capacity to design, manufacture and test transformers up to 160 MVA .
2. Plant is capable to produce and test 245 kV Transformers.
3. Annual manufacturing capacity of 7000MVA per annum.
Testing Facility
1. Equipped with state of the art testing facilities to perform all routine and special tests for transformers up to 160 MVA/220 KV class.
2. 1200 kvp impulse generator for carrying out impulse test.
3.Capacitor Bank for Load Loss Test for higher capacity.
4. Voltage Divider for higher Voltage Test
Process / Equipment
- 16 Horizontal winding machines of capacity ranging from 5T to 10 T and 3 Vertical winding machines of 10 T capacity.
- 08 Horizontal Winding machines and 03 winding machines are installed in a room with positive pressure.
- There are 02 Nos. of VPDs for processing of active parts, 01 no. of vacuum drying plant for processing of Separate Phase Assemblies and 01 no. of vacuum oven for processing of windings.
- 200T capacity hydraulic press for pressing of windings.
- Low humidity room for final pressing of active part before tanking